DUDHI GYPSUM PLASTERING OVERVIEW
Gypsum plastering is an alternative to traditional sand-cement applications for internal plastering surfaces.
Gypsum plaster, also known as Dudhi plaster, is made from gypsum, a naturally occurring mineral that is abundant in nature. The plaster consists of gypsum powder mixed with water, which is then applied to walls and ceilings to create a smooth, flat surface.
Dudhi plastering has become increasingly popular in recent years due to its many benefits. It is lightweight and easy to handle, making it easier to work with than traditional plaster. Dudhi plaster also has superior sound insulation properties and is fire resistant, making it a popular choice for commercial buildings and homes alike.
In addition to these benefits, Dudhi plaster is also more environmentally friendly than traditional plaster. It contains fewer harmful chemicals and produces less waste during the application process. This means that it has a lower impact on the environment and is a more sustainable choice for builders and homeowners.
Overall, Gyproc plastering is a high-quality, versatile, and practical option for internal plastering surfaces. Its environmentally friendly properties make it an ideal choice for those looking to reduce their carbon footprint and create a more sustainable living environment.
What is gypsum plaster?
Gypsum plaster is a type of plaster that is made from gypsum, a soft mineral made up of calcium sulfate dihydrate. It is commonly used as a wall and ceiling covering due to its durability, fire resistance, and smooth finish. Gypsum plaster is also known as plaster of Paris, as it was historically made from the large gypsum deposits found near Paris, France. Today, it is manufactured by heating gypsum to remove the water content and then grinding it into a fine powder that can be mixed with water to form a paste. This paste can then be applied to surfaces and allowed to dry, creating a smooth and even finish.
- Gypsum rock(CaSO4.2H2O) when heated to 150 -250°C looses ¾ of its water. Gypsum rock gets converted in CaSO4.½H2O(POP).
- CaSO4.2H2O → CaSO4.½H2O(POP) + 3/2 H2O
- CaSO4.½H2O(POP) + Aggregate(Vermiculite / Perlite) + Additives → Gypsum
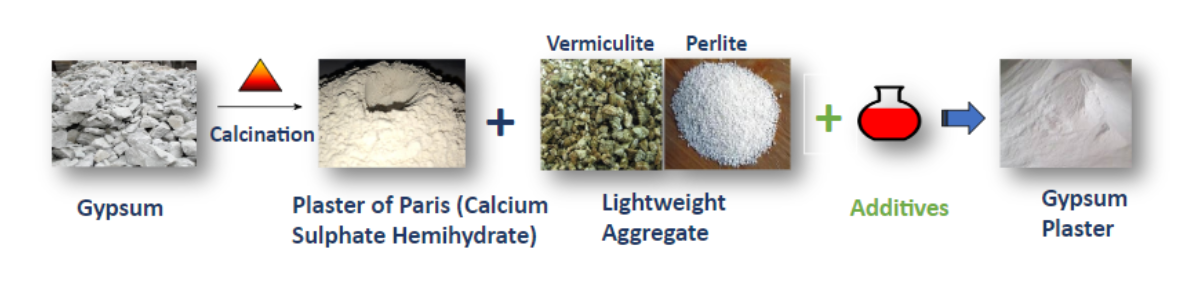
FAQ/TERMS
How Can We Help You
Gypsum plaster is made from a naturally occurring mineral called gypsum, which is found in abundance in many parts of the world. The mineral is heated to a high temperature and then ground into a fine powder. When mixed with water, it forms a paste that can be applied to walls, ceilings, and other surfaces.
One of the advantages of gypsum plaster is that it sets quickly, which makes it ideal for use in modern construction projects where time is of the essence. Unlike traditional cement-based plaster, which can take several days to dry and cure, gypsum plaster can be sanded and painted in just 24 hours.
Gypsum plaster also has excellent fire-resistant properties, which makes it a popular choice for use in commercial and industrial applications. It is also resistant to mold and mildew, which helps to maintain healthy indoor air quality.
In addition to its technical properties, gypsum plaster is also popular because of its aesthetic appeal. It can be easily shaped and molded into decorative designs, which makes it ideal for creating intricate patterns on walls and ceilings.
Overall, gypsum plaster is a versatile and durable material that is well-suited for a wide range of construction applications. Its popularity is likely to continue growing in the coming years as more builders and architects discover its many benefits.
There are various standard testing methods used in India for testing gypsum plaster. Some of these methods are:
- Setting Time: The setting time of gypsum plaster is tested by taking a sample of the plaster and measuring the time it takes to set.
- Compressive Strength: The compressive strength of the gypsum plaster is tested by crushing a sample of the plaster and measuring the force required to break it.
- Bulk Density: The bulk density of the gypsum plaster is tested by weighing a known volume of the plaster and calculating its density.
- Water Absorption: Water absorption of the gypsum plaster is tested by measuring the amount of water absorbed by a known weight of the plaster.
- Flexural Strength: The flexural strength of the gypsum plaster is tested by bending a sample of the plaster and measuring the force required to break it.
- Surface Hardness: The surface hardness of the gypsum plaster is tested by using a sclerometer or similar device to measure the hardness of the surface.
- Fineness Test: The fineness of the gypsum plaster is tested by passing it through a sieve and measuring the amount that passes through a particular size of mesh.
These testing methods are used to ensure that the gypsum plaster is of high quality and meets the required standards. Gypsum Plasters are tested on the basis of their physical and chemical properties. These tests are revised into two parts:
Part I deals with all Gypsum Plasters with or without “light weight aggregates”. This method covers the tests determining Normal consistency (%), setting time (minutes), compressive strength (N/mm2), transverse strength (N/mm2), soundness, expansion (%), freedom from coarse particles (residue on 150micron mesh) & bulk density (kg/M3).
Part II deals with Gypsum Plaster containing premixed “lightweight aggregates” and necessarily complying to IS: 2547 (Part 1).
Performance |
Description | Sand Cement Plaster | Dudhi Plaster (POP) | Dudhi Gypsum (Brick Solution) |
Direct Application (Brick/Block/RCC) | ✔ | X | ✔ |
Line & Level | X | ✔ | ✔ |
Time Saving | X | X | ✔ |
Smooth Finish | X | ✔ | ✔ |
Quality Assurance | X | ✔ | ✔ |
Water Curing | ✔ | Does not Require | Does not Require |
Shrinkage Cracks | ✔ | Does not Appear | Does not Appear |
In-House Manufacturing | X | ✔ | ✔ |
Particular | Sand Cement Plaster (Rs.) | P.O.P. (Rs.) | Cement Plaster + P.O.P. (Rs.) | Dudhi Gypsum (Brick Solution) (Rs.) |
Thickness in (mm) | 14-15 | 7-8 | 21-22 | 20-22 |
Material Cost / Sq.Ft. | 08-09 | 06-07 | 15-16 | 12-13 | Labour Cost / Sq.Ft. | 06-07 | 06-07 | 12-13 | 11-12 | Total Cost / Sq.Ft. | 15-16 | 12-13 | 28-29 | 23-25 | Net saving cost per Sq.Ft. | 04-05 |
Thickness in mm | 11-15 | 16-20 | 20-22 |
Consumption / Sq. Ft. | 1.300 kg | 1.600 kg | 1.900 kg |
- Strength and durability: Gypsum plaster is stronger and more durable than plaster of Paris, making it suitable for installation in high traffic areas or rooms where moisture is present.
- Resistance to cracking: Gypsum plaster has a lower tendency to crack than plaster of Paris, which can crack and chip easily if exposed to excessive force or vibrations.
- Fire resistance: Gypsum plaster is more fire resistant than plaster of Paris, which can be damaged or burned in high temperatures.
- Smooth finish: Gypsum plaster produces a smoother and more polished finish compared to plaster of Paris, which tends to be more rough and textured.
- Eco-friendliness: Gypsum plaster is more eco-friendly than plaster of Paris, as it is made from natural materials and does not require high energy inputs for manufacturing.
- Cost-effectiveness: Gypsum plaster is generally more cost-effective than plaster of Paris, as it requires less material and labor for installation.
As an AI language model, I do not have knowledge of the specific type of paint or gypsum being used, but in general, it is recommended to wait at least 24-48 hours before painting over gypsum or any other type of patching or repair material. This will allow sufficient time for the material to dry and cure properly. However, it is important to follow the manufacturer’s instructions and any specific recommendations for the particular product being used
- Start by preparing the surface by removing any loose or flaky materials, dust, and debris.
- Apply a rendering coat of plaster to the surface using a trowel. The thickness of the coat should be even and around 8-10mm.
- Once the rendering coat is dry, use a straight edge or spirit level to check for any unevenness or rough patches. Mark these areas.
- Apply a second coat of plaster to the marked areas using a trowel, focusing on building up the plaster to create a flat and even surface. Ensure that this second coat is slightly thicker than the first coat to allow for levelling.
- Use a straight edge, like a plasterer’s rule, or a level to check the surface again. Repeat the process if necessary.
- Once the surface is flat and even, allow the plaster to dry completely.
- Finally, sand the surface to achieve a smooth finish, ready for painting or wallpapering.
- Eliminates two-step process of Sand Cement Plaster and POP punning
- Doesn’t require water curing
- No shrinkage cracks
- Non-combustible (when tested in accordance with BS: 476: part 4:1970), therefore a good form of thermal protection to the building structure.
Use of light weight aggregates in the plaster mix help to improve Low thermal conductivity (0.25 W/m2K) as compared to Sand Cement Plaster (0.72 W/m2K) ** keeps room cooler in summer and warmer in winter; saving in energy cost
The water absorption as per DIN EN 520 is less ≤10%
- Excellent Capillary
- Water absorption coefficient test method – BS EN 1015-18.
*Above parameters are tested under lab conditions. Actual performance depends on site usage, conditions and working
Calcium Sulphate Hemihydrate: CaS04. ½ H2O
Approx. 6 months from the date of manufacturing when stored in dry conditions
Consumption Per mm/ Per Sq. Ft.- 0.100 kg.
Coverage 13mm Thickness 30 sq-ft/40 kg bag, 19 sq-ft/25 kg bag
Storage & Handling
Dudhi Gypsum (Brick Solution) (Moisture Resistant) is supplied in 40Kg bags. The dimensions of the bag ensure that a well-filled appearance is presented when filled and the bags can be stacked on a pallet in a stable and well-stacked array. Bags should be stored dry, as absorption of water shortens the setting time, causes set lumps to form in the bags and may reduce the strength of the set plasterwork. No hooks or any sharp tools should be used to carry bags from one location to another.
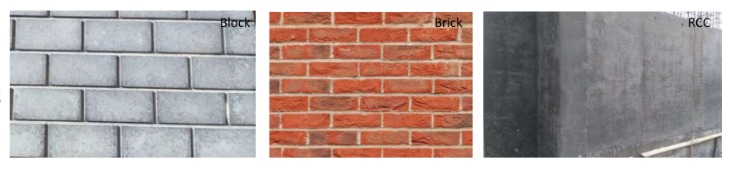
Surfaces should be completely clean, reasonably dry, protected from the direct exposure from weather and suitable for the chosen specification. In addition, before plastering concrete backgrounds, ensure that any mould oil or Concrete Curing Agent (other agents) present are removed from the surface. No-fines concrete does not require wetting prior to plastering. Plaster should not be applied onto a ‘green’ background or when any free water is visible. Clean water should be applied 5-10 minutes before plaster application to control the suction. In-situ or pre-cast concrete which are exceptionally smooth or having low suction will require pre-treatment with Dudhi Plaster Bond bonding agent.
- Dissimilar expansion and contraction of RCC and brick / stone masonry could cause stresses and at times separation. To reduce the separation cracks, use of 145 GSM glass fiber mesh (at the junction) is recommended.
- It is not suitable for use in long continuously damp or severely humid conditions
- If Gypsum Plaster is to be applied on RCC surfaces with the thickness of the application being more than 15 mm then It is to be applied only when moisture is very low and the temperature is more than 10 degrees Celcius because RCC construction has almost negligible porosity as compared to NON-RCC SURFACES. Hence it cannot absorb water.
In case Dudhi Gypsum (Brick Solution) is applied on internal walls but the exterior cement plaster work of the same wall is pending then Cement Plaster work must be completed prior to painting of the internal walls. Any seepage of moisture during curing from outside will from escape surface of the Gypsum plaster. Please note that the escaping water from Dudhi Gypsum (Brick Solution) may leave some green spots on the surface which can be easily removed with the help of sand paper and then Paint work of the internal walls should be done.
It is not suitable for use in long continuously damp surfaces. For application make the substrate dry and then application to be made.
The information herein should not be read in isolation as it is meant only as guidance for the user, who should always ensure that they are fully conversant with the products and systems being used and their subsequent installation prior to the commencement of work.
Gypsum is effective in fire because it contains a high percentage of water in its chemical composition, which when heated releases as steam and helps to slow down or prevent the spread of fire. The water acts as a coolant and reduces the temperature of the surrounding area, preventing the ignition of nearby combustible materials. Additionally, when gypsum is used in building construction, it can act as a barrier between different areas of the building, preventing the spread of fire within the walls or ceiling. Gypsum is also non-combustible, which means that it does not burn or contribute to the spread of fire. This makes it an ideal material for fire-resistant walls, ceilings, and partitions in buildings.